在塑料加工和聚合物改性领域,实验室双螺杆挤出机作为研发的重要工具,因其卓越的可调性、精确的控制能力和广泛的应用范围,成为了实验室研究和产品开发中不可或缺的设备。螺杆设计的优化是提升双螺杆挤出机性能的核心因素之一。本文将深入探讨如何通过合理的螺杆设计,充分发挥实验室双螺杆挤出机的潜力,帮助实验室实现高效、稳定的物料加工过程。
1. 双螺杆挤出机的基本构造与工作原理
实验室双螺杆挤出机由两根相互旋转的螺杆组成,主要用于物料的输送、混合与塑化。与传统的单螺杆挤出机相比,双螺杆挤出机能够提供更高效的物料混合、更均匀的熔体流动及更高的加工性能。这种设备的结构是模块化的,能够根据不同的工艺要求,通过更换螺纹元件来调整性能。螺杆设计通常分为多个功能区段,例如加料段、固体输送段、熔融段、混合段、排气段等。每个段落的螺纹设计和优化都直接影响挤出机的整体性能。
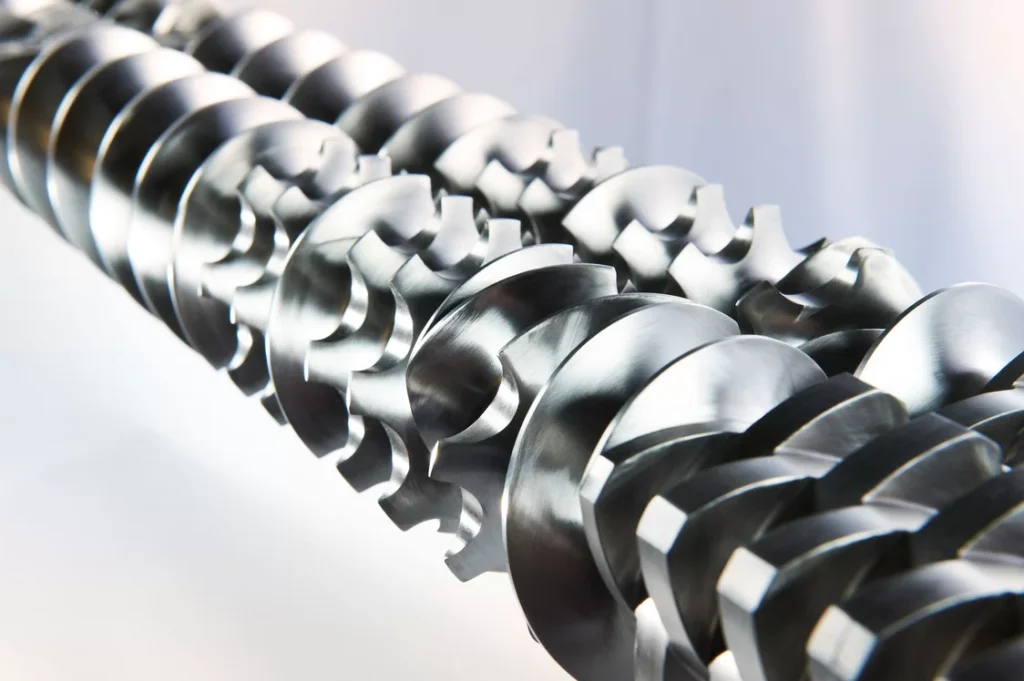
2. 加料段的螺杆设计
加料段是双螺杆挤出机中至关重要的部分,负责将物料顺利地输送到下游加工区域。为了保证物料的顺利加入,设计时通常使用大导程的正向螺纹元件。这些螺纹元件能够增加物料的容积并提高输送效率。
对于不同物料,加料段的螺杆设计需有所调整。例如,低密度粉料和纤维状物料常使用深螺槽的大导程螺纹元件,以防止卡料或堵塞的现象。实验研究显示,采用这种设计后,物料输送能力通常能够提升20%至30%。
3. 固体输送段的螺杆设计
固体输送段的主要任务是将已加入的固体物料有效地输送,同时提高物料的充填密度,从而有助于后续的熔融和塑化过程。在这一段,常常使用大导程和小导程螺纹元件的组合设计。通过从大导程到小导程的过渡,物料在输送过程中会逐渐被压缩,增强物料的充填密度,为熔融过程提供良好的条件。
此类设计显著提高了物料的压实效果,使物料在输送过程中能够达到更高的填充密度,进一步加速了熔融过程。
4. 熔融塑化段的螺杆设计
熔融塑化段是双螺杆挤出机的核心部分之一,主要任务是通过机械剪切和外部加热将固体物料转化为均匀的熔体。为了提高熔融效率,熔融段的螺杆设计需能够有效地将机械能转化为热能,并确保物料的均匀熔化。
在设计上,熔融段通常采用啮合块、反向螺纹元件和非对称大导程螺纹元件的组合。通过这些设计,不仅能提高物料的剪切力,还能加快熔融速度。实验数据表明,采用这种组合设计的实验室双螺杆挤出机比传统设计的熔融效率提升了40%至50%。
反向螺纹元件在这一段的使用,可以有效地控制熔体的压力,避免熔体温度过高,从而减少聚合物降解的风险。
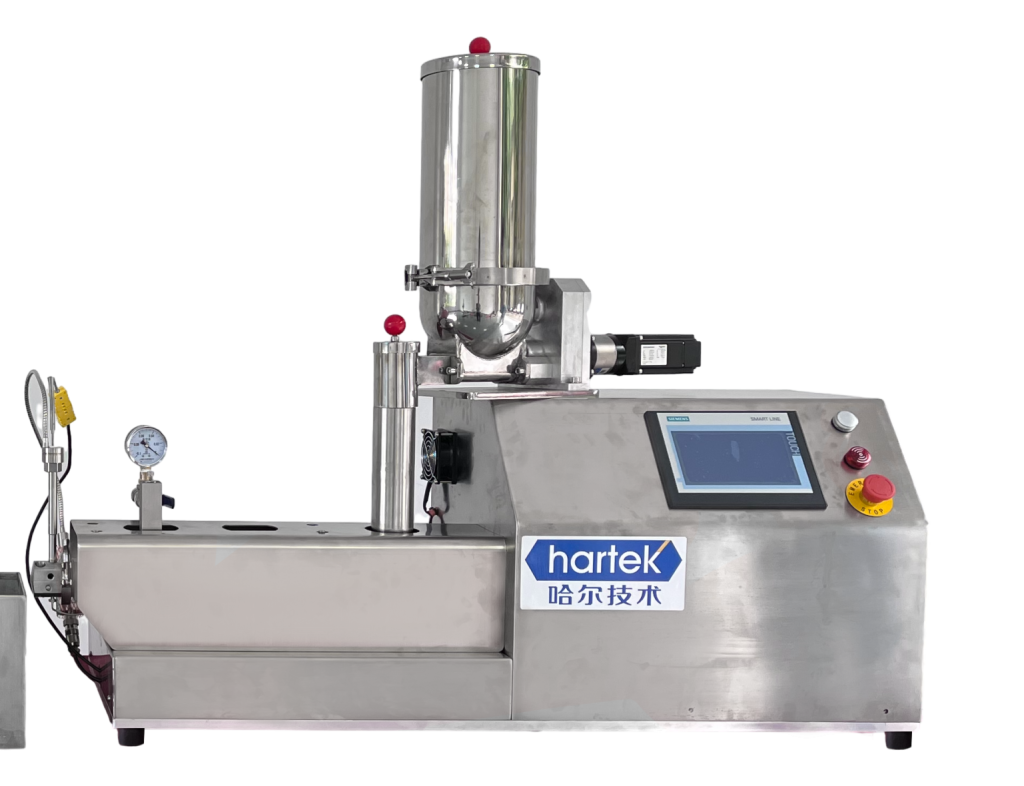
5. 排气段的螺杆设计
排气段的主要功能是通过加热和高压将物料中的气体、水分及其他挥发性物质排出,从而保证最终产品的纯度和质量。为了提高排气效果,排气段设计中通常使用大导程的螺纹元件与密封元件组合。
这些设计可以降低物料的充填度,增加物料与螺杆之间的自由表面积,进一步促进湿气和气体的排出。实验结果表明,优化的排气段设计能够将物料中的水分和挥发性组分降低10%至20%,显著提高产品的质量。
6. 混合段的螺杆设计
混合段是双螺杆挤出机中最为关键的部分之一,主要作用是确保物料均匀混合。为了提高混合效果,通常使用啮合块、涡轮混合元件和反向螺纹元件等多种元件组合。通过这些设计,可以显著提高物料的混合强度,改善物料的分散效果。
7. 螺杆设计对实验室双螺杆挤出机性能的影响
实验数据表明,螺杆设计对双螺杆挤出机的性能影响显著。优化的螺杆设计能够提高物料的输送效率、熔融均匀性、混合效果以及排气效果。而不合适的设计则可能导致设备负荷过大、温度不均匀、熔体不稳定等问题,进而影响产品质量。例如,优化后的螺杆设计可将熔融时间减少40%以上,物料输送能力提升10%至20%。同时,合理的排气设计有助于减少湿气含量,从而避免气泡的生成。
结语
螺杆设计和优化对于实验室双螺杆挤出机的性能至关重要。通过合理分析各个功能段的螺杆设计,并根据物料特性进行调整,可以显著提升挤出机的整体性能和效率。随着材料种类的多样化和工艺要求的提高,双螺杆挤出机的螺杆设计将不断向精细化、高效化发展。希望本文的分析能为从事相关领域研发的工程师提供有价值的参考,助力高效、精确的挤出加工。
广州市哈尔技术有限公司致力于研发和制造小型实验用塑料加工成型设备,我们为客户提供全面的技术咨询、提供完善的解决方案和实验室建设企划。
哈尔最畅销的产品包括:小型挤出机、小型流延膜机、小型吹膜机、小型片材挤出压延机、小型双螺杆挤出机、热熔双螺杆挤出机、小型三辊压延机、小型密炼机和小型双辊开炼机等。实验室塑机产品功能齐备,操作简易、扩展方便,可应用于配方研发、工艺优化、质量控制、创新研究、设计指导、技工和学生培训等用途,适合于专业院校从事高分子材料(塑料、橡胶)的研究、塑料加工业企业的产品研发或生产部门的质量控制,以及专业学校的技术培训等用途。